- Joined
- May 24, 2023
- Messages
- 1,199 (1.66/day)
I examined Alphacool CORE 1 CPU block which I got a few weeks ago directly from the manufacturer, the block package has a little round sticker on it indicating, that the block may have been made in January 2024.
I inspected the block using my ink method described here:
How to check flatness of CPUs and coolers - INK and OPTICAL INTERFERENCE methods | TechPowerUp Forums
and found out that the block has an extremely strong bulge in the middle:
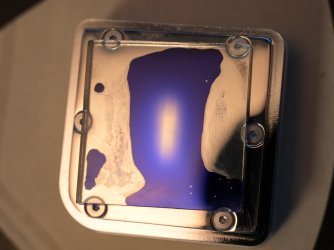
After inspecting it closer I found, that the block surface is deformed along the water channel cuts, you can see that here:
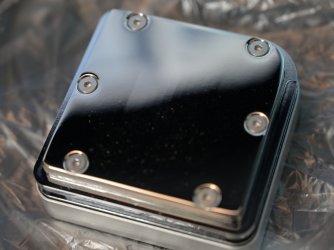
Especially on the outer edges the change of shape is so notable, that I fear the the block may split in those areas. This is obviously caused by the water channels being cut very deep and leaving little material to maintain mechanical integrity of the base. Another cause is a thick rubber sheet stuffed under the base, which has marks on it proving that it is subjected to high pressure.
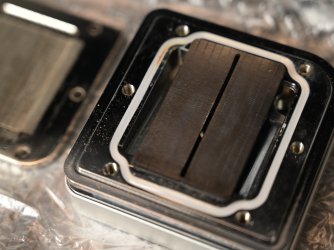
I tried removing the sheet and running the block without it. The bulge disappeared, but I could not judge the flatness because of the raised parts in the corners:
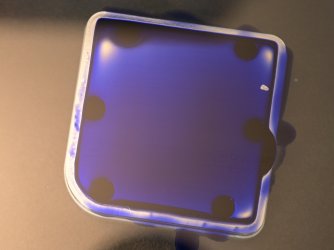
In any case, the paste imprints after removing the block from the CPU look good:
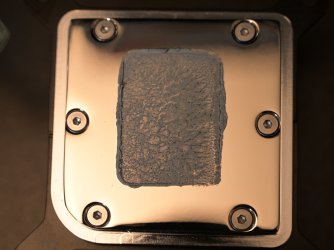
Compare that to the original imprints of the bulging block:
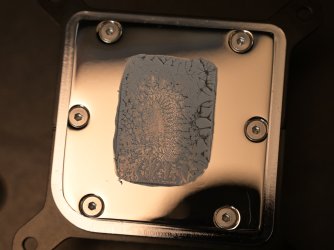
You can see a thin layer of the paste just in the area of the bulge, and very thick layer of the paste especially on the right ride.
I performed a test with heat load of 253W. The temperature under the same conditions (average over all cores) was 68-69°C with the original bulging block and a degree higher with the rubber sheet completely removed and better block to CPU contact. Removing the rubber sheet may have caused some water to bypass the cooling channels and flow above them.
I am convinced that with the rubber sheet that is thinner and will not cause so extreme pressure build-up under the base and bulging and a bit shallower water channel cuts improving mechanical base integrity the performance of the block would be close to the same as of the current version of the block, which is bursting at the seams.
I noticed that the block with no other signs of use had such bubbles under the protective foil, that happen when you remove the foill and return it. Is somebody in Germany inspecting the blocks when they arrive from the manufacturer, if they are not close to splitting - you could recognise it by how sharp those deformation edges on the surface would appear.
Have you heard about a case when this block split?
Is my block a lemon, or are all these blocks like this?
If they are intended to be made this way, I really do not think it was a good idea.
I inspected the block using my ink method described here:
How to check flatness of CPUs and coolers - INK and OPTICAL INTERFERENCE methods | TechPowerUp Forums
and found out that the block has an extremely strong bulge in the middle:
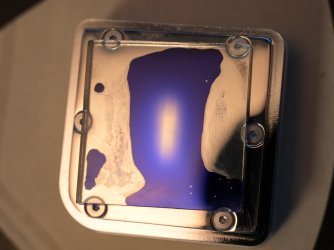
After inspecting it closer I found, that the block surface is deformed along the water channel cuts, you can see that here:
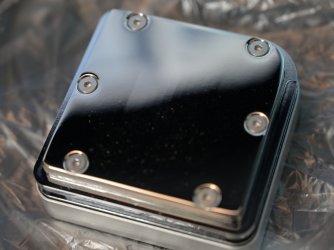
Especially on the outer edges the change of shape is so notable, that I fear the the block may split in those areas. This is obviously caused by the water channels being cut very deep and leaving little material to maintain mechanical integrity of the base. Another cause is a thick rubber sheet stuffed under the base, which has marks on it proving that it is subjected to high pressure.
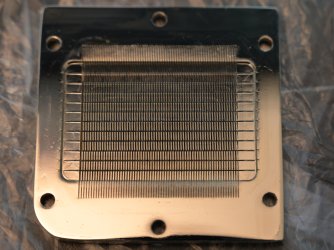
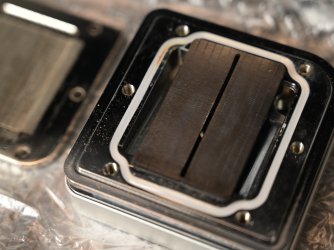
I tried removing the sheet and running the block without it. The bulge disappeared, but I could not judge the flatness because of the raised parts in the corners:
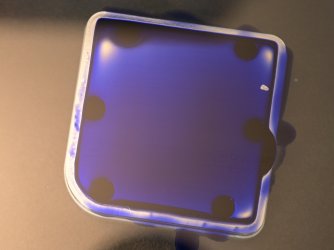
In any case, the paste imprints after removing the block from the CPU look good:
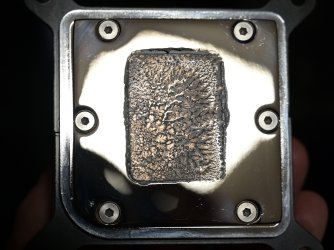
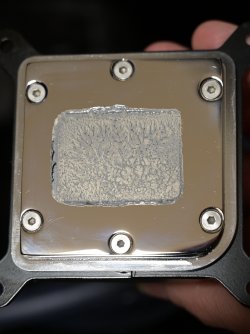
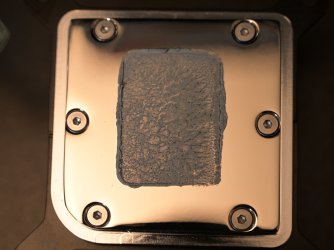
Compare that to the original imprints of the bulging block:
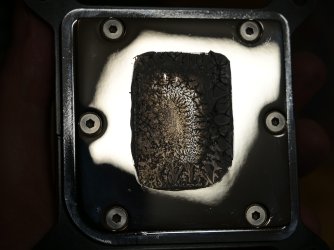
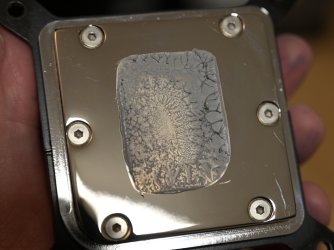
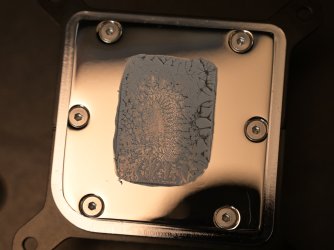
You can see a thin layer of the paste just in the area of the bulge, and very thick layer of the paste especially on the right ride.
I performed a test with heat load of 253W. The temperature under the same conditions (average over all cores) was 68-69°C with the original bulging block and a degree higher with the rubber sheet completely removed and better block to CPU contact. Removing the rubber sheet may have caused some water to bypass the cooling channels and flow above them.
I am convinced that with the rubber sheet that is thinner and will not cause so extreme pressure build-up under the base and bulging and a bit shallower water channel cuts improving mechanical base integrity the performance of the block would be close to the same as of the current version of the block, which is bursting at the seams.
I noticed that the block with no other signs of use had such bubbles under the protective foil, that happen when you remove the foill and return it. Is somebody in Germany inspecting the blocks when they arrive from the manufacturer, if they are not close to splitting - you could recognise it by how sharp those deformation edges on the surface would appear.
Have you heard about a case when this block split?
Is my block a lemon, or are all these blocks like this?
If they are intended to be made this way, I really do not think it was a good idea.
Last edited: